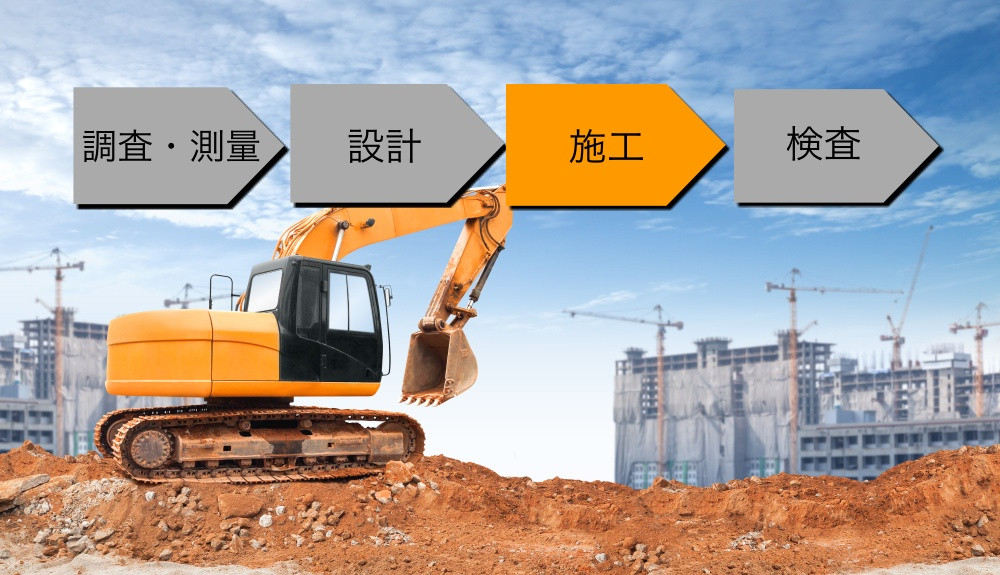
あらゆる建設事業は「調査・測量、設計、施工、検査」という一連のプロセスを辿る。本記事では「施工」の現場で、どのようにICT技術が活用されているのかについて紹介していく。
施工現場にICT技術が導入される以前は、設計図面を施工現場に落とし込む「丁張り」という工程が必須であった。ただ職人の経験とスキルに依存してきたために、技術継承がスムーズに進まないケースが様々な現場で散見されてきた。こうした施工現場の課題を解決し、作業品質の向上を実現するのがICT施工だ。
ICT施工は、3次元データを活用して建機によって施工するもので、使われる建機は2種類に大別される。建機を自動制御する「マシンコントロールシステム(MC)」と建機のオペレーターをサポートする「マシンコントロールガイダンスシステム(MG)」だ。
最初に「マシンコントロールシステム(MC)」の概略を説明していく。測量、そして設計のプロセスで作成された3次元データを、ICT建機に読み込ませることで、建機を自動制御する方法だ。
高精度GNSSなどを用いて位置情報を同時に読み込むため、施工現場で必須とされてきた丁張り作業が不要となる。さらに、3次元データ上の座標通りに操作が行われるため、建機操作の習熟度が低いオペレーターであっても設計図面通りの施工が可能になった。
Shutterstock
例えば油圧ショベルの場合、アーム操作技術にはオペレーターの習熟度が大きく影響していた。それがICT化によりアーム制御システムが搭載され、操作のセミオート化が実現したのだ。
ブルドーザであれば、掘削箇所の調整やブレードを下げる深さなどの操作技術はオペレーターに依存していた。それがICT化により、粗掘削から仕上げ作業まで自動ブレード制御機能が搭載された。車両を前後左右に動かすという簡単な操作のみで、設計図通りの施工を行えるようになったのだ。
一方「マシンガイダンスシステム(MG)」だが、MGを説明するのに、よく例えられるのが“カーナビ”だ。現在地と目的地(設計データ)の距離をオペレーターに示すのが主な働きで、オペレーターは自分で建機を操作する必要がある。
仕組みとしては、地上で位置計測する「自動追尾式トータルステーション(TS)」や人工衛星による位置計測の「GNSS」などが、建機の位置をリアルタイムで計測し、オペレーターに送信。カーナビのように位置情報を確認しながら作業を進めることができるため、丁張り工程が不要となる上に、何人もの作業員を導入して行われてきた作業箇所の確認時間も大幅に軽減する。
Shutterstock
とくに、地中に送電線やガス管、水道管など多くの埋設物のある施工現場では、建機と埋設物の接触を避けるため、何度も図面と施工現場の位置を確認する必要があり、安全の確保に多大な時間を要していた。
それが、マシンガイダンスシステム(MG)を利用することで、建機内に設置したタブレット端末上で作業箇所と埋設物の位置を確認できるようになり、安全確保と施工作業を同時に行えるようになった。
またマシンガイダンスシステム(MG)は、その導入の手軽さも魅力の一つだ。システムを搭載した機器を後付けで設置すれば、既存の建機でもマシンガイダンスシステム(MG)を利用することができるため、新たにICT建機を購入する必要はない。ICT化に抵抗のある熟練オペレーターの方にも、使い慣れた建機でICT施工の利便性を感じていただけるかと思う。
ICT施工により、品質管理、そして技術継承を実現
Shutterstock
施工現場におけるデータ活用は、品質管理にも役立てることができる。施工時に3次元データを読み込むだけでなく、作業内容を記録することができるため、データをトラブル発生時に活用することができる。記録を振り返り、いつ、何が原因でトラブルが起こったのか、すぐに原因を究明することで、迅速な対応が可能になり、施工計画への影響を最小限に抑えることができるのである。
施工の完全無人化を実現するため、現在大手建機メーカーや建設会社によって、革新的な技術開発が進められている。さらに昨今はスタートアップ企業の参入も著しく、とくにAI(人工知能)の学習機能を利用した、建機の自動運転技術の実用化に大きな期待が寄せられている。建設DXを加速させていく、ICT施工の現場から目が離せない。
施工現場にICT技術が導入される以前は、設計図面を施工現場に落とし込む「丁張り」という工程が必須であった。ただ職人の経験とスキルに依存してきたために、技術継承がスムーズに進まないケースが様々な現場で散見されてきた。こうした施工現場の課題を解決し、作業品質の向上を実現するのがICT施工だ。
ICT施工は、3次元データを活用して建機によって施工するもので、使われる建機は2種類に大別される。建機を自動制御する「マシンコントロールシステム(MC)」と建機のオペレーターをサポートする「マシンコントロールガイダンスシステム(MG)」だ。
技術面の課題を解決するマシンコントロールシステム(MC)
最初に「マシンコントロールシステム(MC)」の概略を説明していく。測量、そして設計のプロセスで作成された3次元データを、ICT建機に読み込ませることで、建機を自動制御する方法だ。
高精度GNSSなどを用いて位置情報を同時に読み込むため、施工現場で必須とされてきた丁張り作業が不要となる。さらに、3次元データ上の座標通りに操作が行われるため、建機操作の習熟度が低いオペレーターであっても設計図面通りの施工が可能になった。
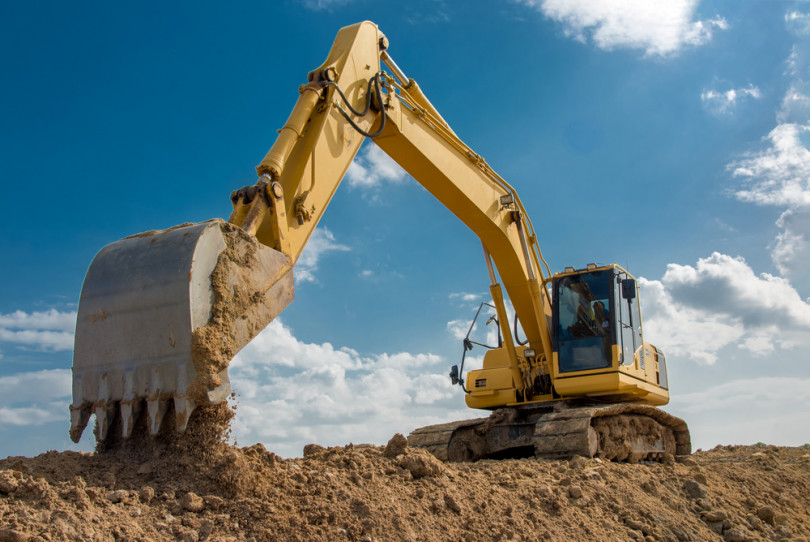
例えば油圧ショベルの場合、アーム操作技術にはオペレーターの習熟度が大きく影響していた。それがICT化によりアーム制御システムが搭載され、操作のセミオート化が実現したのだ。
ブルドーザであれば、掘削箇所の調整やブレードを下げる深さなどの操作技術はオペレーターに依存していた。それがICT化により、粗掘削から仕上げ作業まで自動ブレード制御機能が搭載された。車両を前後左右に動かすという簡単な操作のみで、設計図通りの施工を行えるようになったのだ。
施工現場の人手不足を解決するマシンガイダンスシステム(MG)
一方「マシンガイダンスシステム(MG)」だが、MGを説明するのに、よく例えられるのが“カーナビ”だ。現在地と目的地(設計データ)の距離をオペレーターに示すのが主な働きで、オペレーターは自分で建機を操作する必要がある。
仕組みとしては、地上で位置計測する「自動追尾式トータルステーション(TS)」や人工衛星による位置計測の「GNSS」などが、建機の位置をリアルタイムで計測し、オペレーターに送信。カーナビのように位置情報を確認しながら作業を進めることができるため、丁張り工程が不要となる上に、何人もの作業員を導入して行われてきた作業箇所の確認時間も大幅に軽減する。
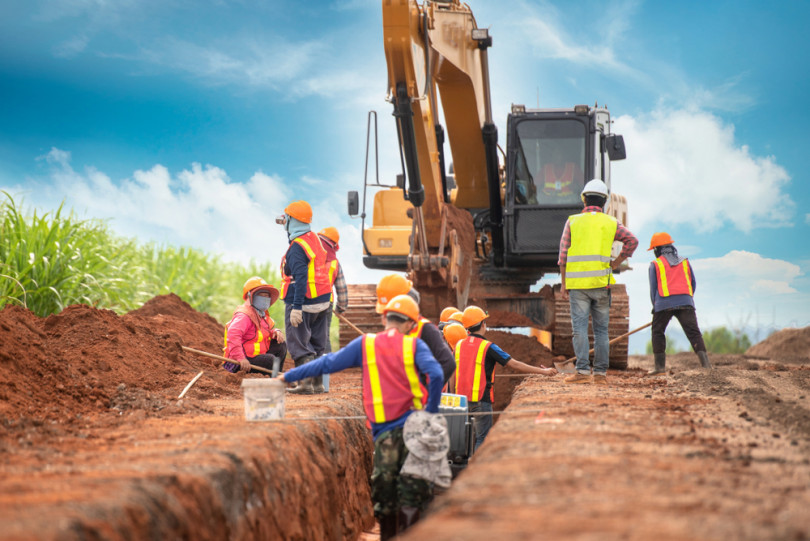
とくに、地中に送電線やガス管、水道管など多くの埋設物のある施工現場では、建機と埋設物の接触を避けるため、何度も図面と施工現場の位置を確認する必要があり、安全の確保に多大な時間を要していた。
それが、マシンガイダンスシステム(MG)を利用することで、建機内に設置したタブレット端末上で作業箇所と埋設物の位置を確認できるようになり、安全確保と施工作業を同時に行えるようになった。
またマシンガイダンスシステム(MG)は、その導入の手軽さも魅力の一つだ。システムを搭載した機器を後付けで設置すれば、既存の建機でもマシンガイダンスシステム(MG)を利用することができるため、新たにICT建機を購入する必要はない。ICT化に抵抗のある熟練オペレーターの方にも、使い慣れた建機でICT施工の利便性を感じていただけるかと思う。
ICT施工により、品質管理、そして技術継承を実現
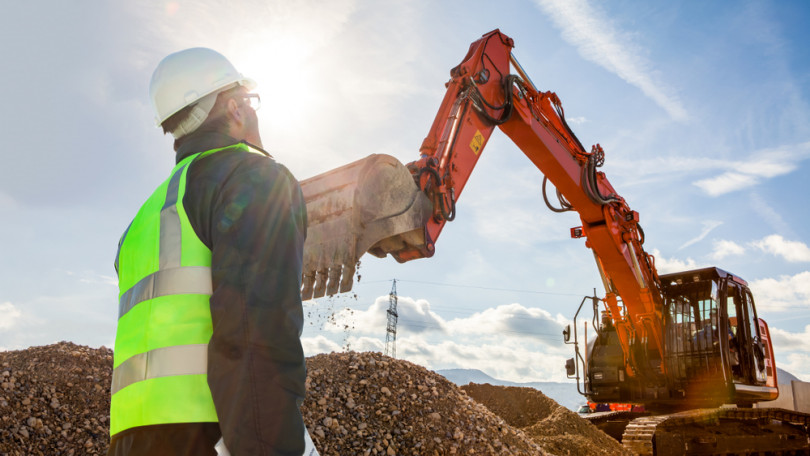
施工現場におけるデータ活用は、品質管理にも役立てることができる。施工時に3次元データを読み込むだけでなく、作業内容を記録することができるため、データをトラブル発生時に活用することができる。記録を振り返り、いつ、何が原因でトラブルが起こったのか、すぐに原因を究明することで、迅速な対応が可能になり、施工計画への影響を最小限に抑えることができるのである。
施工の完全無人化を実現するため、現在大手建機メーカーや建設会社によって、革新的な技術開発が進められている。さらに昨今はスタートアップ企業の参入も著しく、とくにAI(人工知能)の学習機能を利用した、建機の自動運転技術の実用化に大きな期待が寄せられている。建設DXを加速させていく、ICT施工の現場から目が離せない。
WRITTEN by
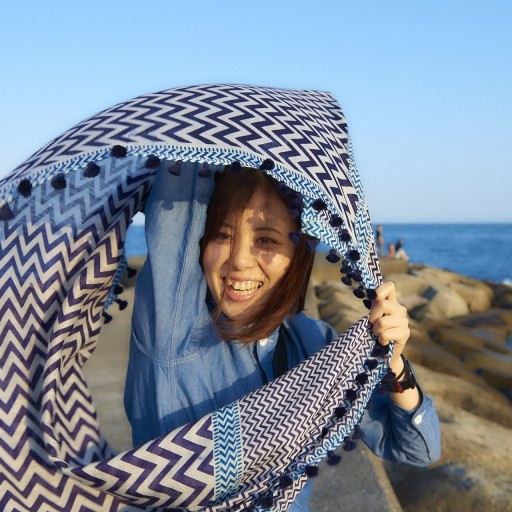
高橋 奈那
神奈川県生まれのコピーライター。コピーライター事務所アシスタント、広告制作会社を経て、2020年より独立。企画・構成からコピーライティング・取材執筆など、ライティング業務全般を手がける。学校法人や企業の発行する広報誌やオウンドメディアといった、広告主のメッセージをじっくり伝える媒体を得意とする。
ICT活用工事の基礎をプロセスごとに紐解く
- ICT施工の現状とは?【ICT活用工事の基礎その3】
建設土木の未来を
ICTで変えるメディア